石墨转子对于密度要求是什么?
常用的除气精炼方法有除气精炼和喷粉精炼。其原理是将惰性气体或精炼剂引入熔炉底部。精炼剂很轻,惰性气体或精炼剂开始从炉底上升。上升过程带走铝液中的氢和浮渣,从而净化铝液。除气用的除气器通过电机带动法兰盘,法兰盘连接石墨转子转动。一般石墨转子使用寿命短,容易被腐蚀坏。为此将石墨转子浸泡在高温高压的介质中,然后烧结固化,提高其使用寿命。这种石墨主要依赖进口,成本高。
旋转喷粉细化效果好,但容易堵石墨转子。生产中使用干燥的惰性气体或高纯氮气进行精炼。气体连接到法兰上,法兰在电机的驱动下开始旋转。石墨转子随法兰转速400 ~ 600 r/min,惰性气体(氩气)流量控制在15 ~ 25 L/min,氮气流量控制在20 ~ 40 L/min。在操作过程中,首先打开空气阀,然后慢慢降低除气器,直到除气器石墨转子与钢包底部之间的距离为100~150 mm。最后,启动电机,开始除气精炼10 ~ 20 min。为了避免石墨转子高速旋转产生的铝液漩涡,在石墨转子的一侧或两侧放置扰流器,以减少旋转过程中铝液的湍流。石墨转子脱气时保证气泡细小、分散度高、效果好,既能保证脱气效果,又能避免气泡打破表面氧化膜而引起沸腾的现象,从而避免二次吸入。脱气后,关闭电机,将石墨转子提离液面,然后关闭空气阀。由于除气前在表面加入除渣剂,除气时产生的铝渣浮在表面,需要敲出渣灰。用专用工具将瓢中的滤液舀出,建议在液面以下快速平稳地倒入两个专用坩埚中。一个坩埚在常压下固化;另一个坩埚迅速盖上钟罩,抽真空,真空压力必须达到8 MPa,抽真空时间为3 ~ 4 min。放入水中冷却,取出晾干,按常压测量密度当量后抽真空。密度当量越小,铝液中的氢含量越低,除气和精炼效果越好。根据不同产品对密度当量的不同要求,不合格的密度当量需要重新细化。
在铝合金熔炼过程中,铝液在精炼前需要进行变质处理。铝液从熔炼炉转移到钢包前,变质剂以合金的形式加入到炉底,变质元素不直接加入。铝锶合金棒常用作变质剂。Sr是一种长效变质剂,作用时间为6 ~ 8 h,使粗大的片状硅细化为细小的组织,力学性能进一步提高。这种改性效果优于将其加入熔炼炉中,并能减少烧损和衰退。Sr炉底熔化后,采用旋转脱气搅拌均匀,减少偏析。Sr变质后的铝液吸氢快,产生许多针孔。精炼后停留时间不宜过长,测氢合格1h以上方可使用。铝液转移到钢包后,撒除渣器,深层搅拌产生渣灰。测量铝液温度是否能达到精炼温度。如果温度过高,则需要添加回炉料来降低温度。如果温度低,就要通电升温。精炼温度应控制在720 ~ 740℃。直到调整合格,在表面撒少量除渣剂。脱气精炼主要涉及脱气和除氢。由于第一次深搅已经去除了大部分夹渣,但里面还有少量铝渣,第二次撒少量除渣剂。
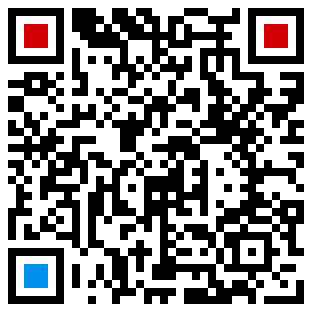